The Craft of Making Traditional British Loafers: Assembly, Lasting, and Finishing
British craftsmanship in shoemaking has long been celebrated for its dedication to quality and tradition. One of the best examples of this is seen in the production of loafers, a timeless classic in men’s footwear. This article delves into the traditional British method of shoemaking, with a particular focus on the processes of assembly, lasting, and finishing, as shared by our manufacturing partner Sanders & Sanders Shoemakers.
1. Assembly: The Foundation
The journey of making a loafer begins with the selection of high-quality cactus leather (our core USP) and other raw materials. In traditional shoemaking, especially in renowned British workshops, the chosen leather is hand-cut into patterns that will later be stitched together to form the shoe's upper. The upper is composed of several pieces, including the vamp (the front part of the shoe), the quarters (side and back), and the apron (the characteristic panel in loafers).
With our loafers, skilled artisans hand-sew these components to ensure durability, which is why no two pairs will be perfectly identical. Each piece of the leather is then meticulously examined to ensure its strength, texture, and appearance are flawless.
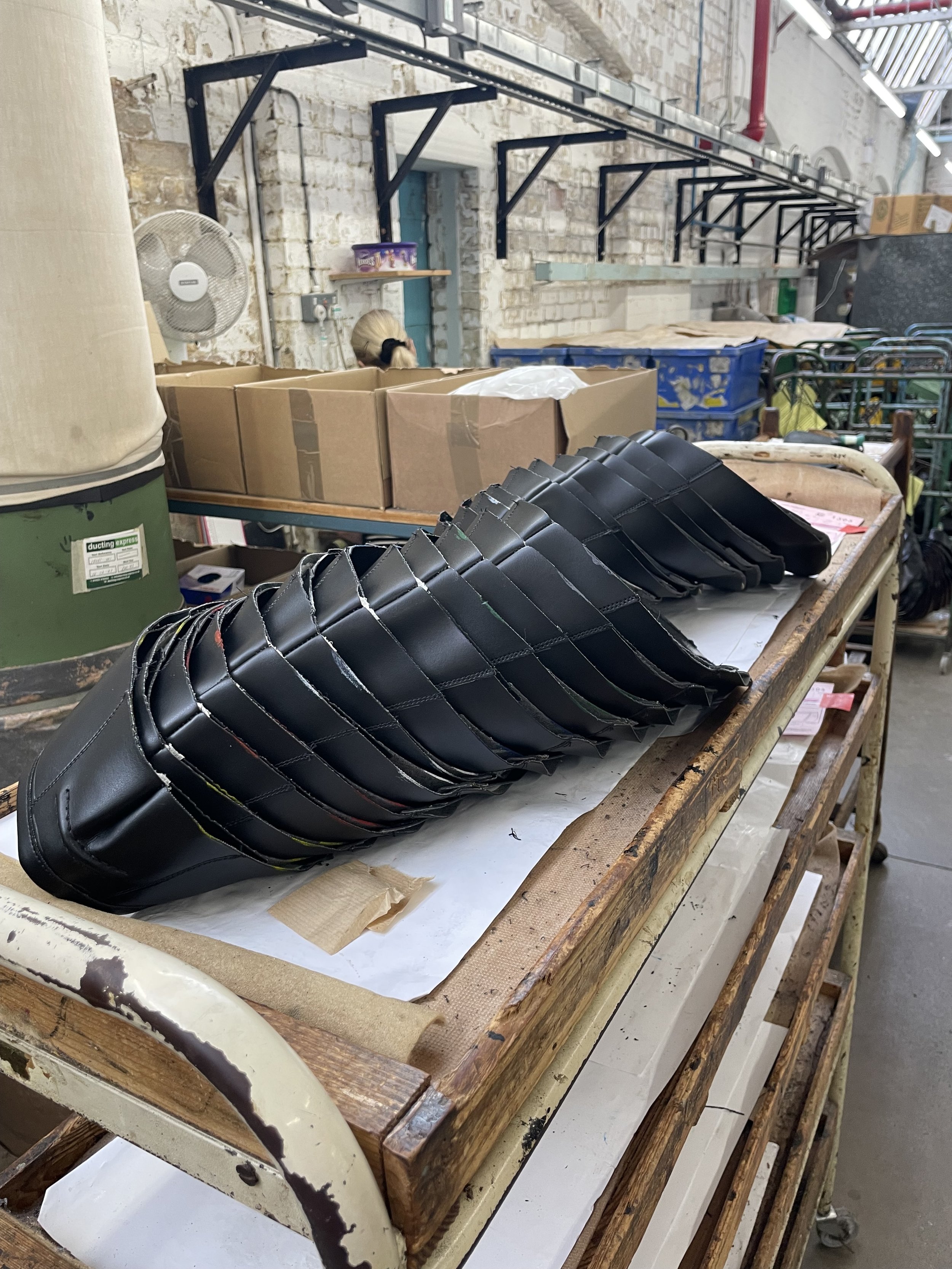

2. Lasting: Giving Shape to the Shoe
The lasting process is where the loafer truly begins to take shape. This involves stretching the upper leather (as per assembly above) over a “last,” which is a wooden or metal mold that defines the shoe’s final shape and size. Lasts are the heart of shoemaking, often regarded as a closely guarded secret, as they determine the comfort and silhouette of the shoe. They can very from slim, to wide; our Fitzroy being the latter thanks to the MATT last we use.
First, the back of the upper is tacked to the heel of the last. The front is then pulled tightly over the last using specialised machinery, ensuring a snug fit around the mold. Precision is critical during this step to ensure that the upper conforms perfectly to the desired form, especially at the toe. Traditional British shoemakers, including us, use a lasting machine with levers, gauges, and sensors, which helps maintain consistency while still requiring the expertise of the artisan to guide the process.
3. Welt Sewing and Bottom Construction
Once the shoe has been lasted, it is time to attach the insole and the welt, a strip of leather stitched around the edge of the upper. Many traditional British loafers are constructed using the Goodyear welting method, a hallmark of quality craftsmanship. This technique involves stitching the welt to both the upper and the insole, allowing the sole to be replaced later without compromising the integrity of the shoe.
The space between the welt and the insole is filled with cork, and a wooden shank is inserted for additional support and comfort. These elements give the loafer structure, durability, and a solid yet flexible base.
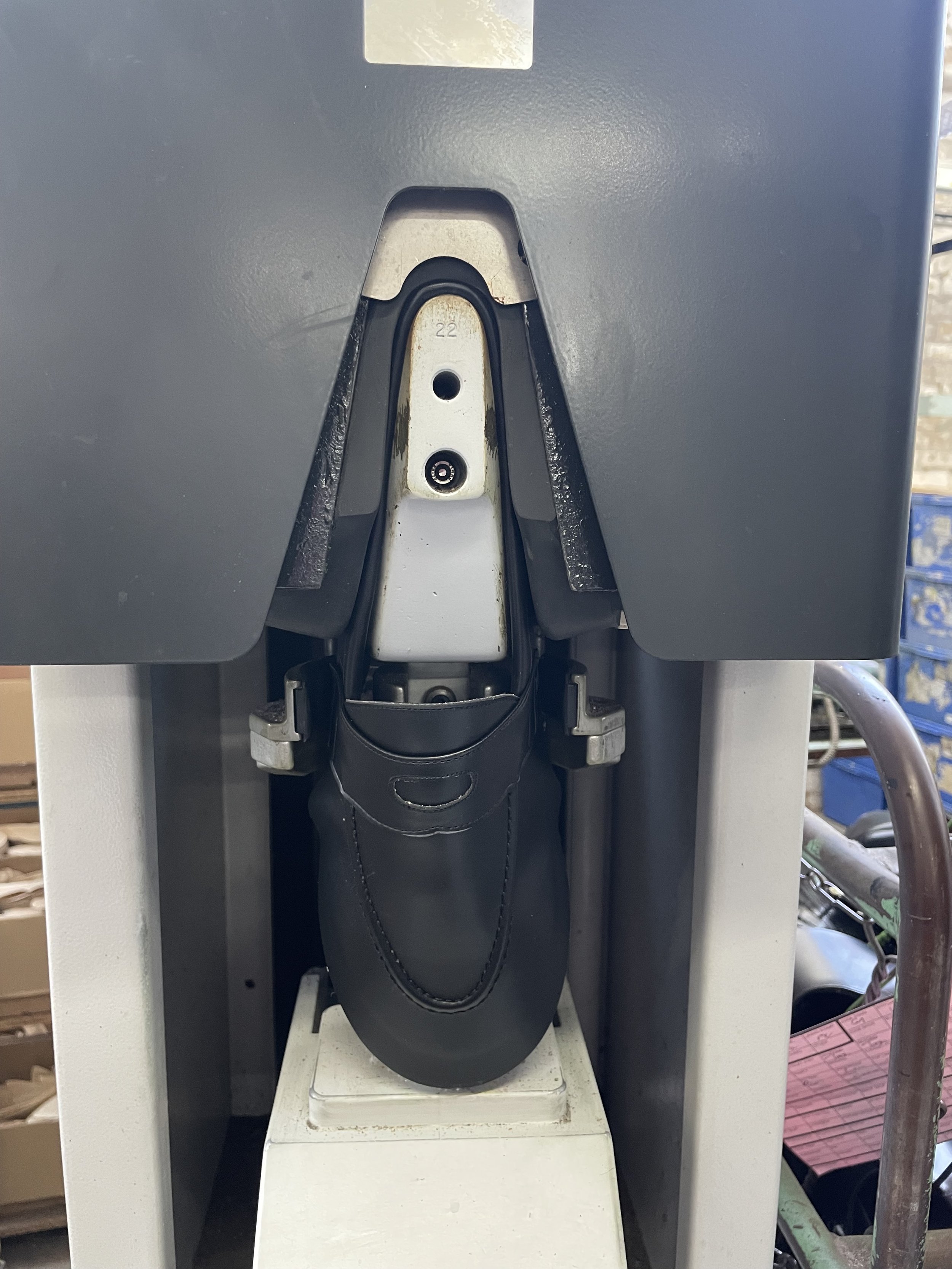
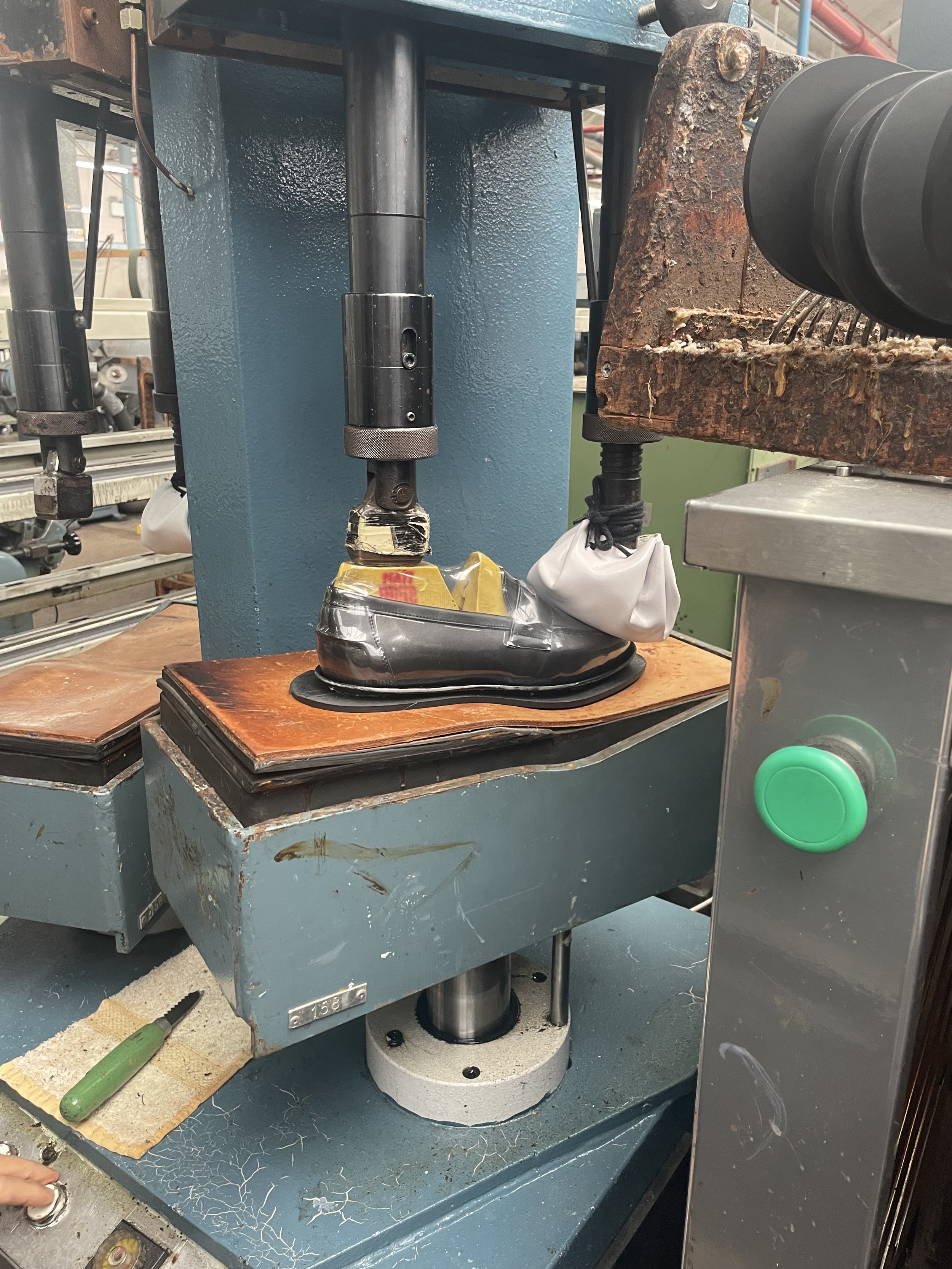
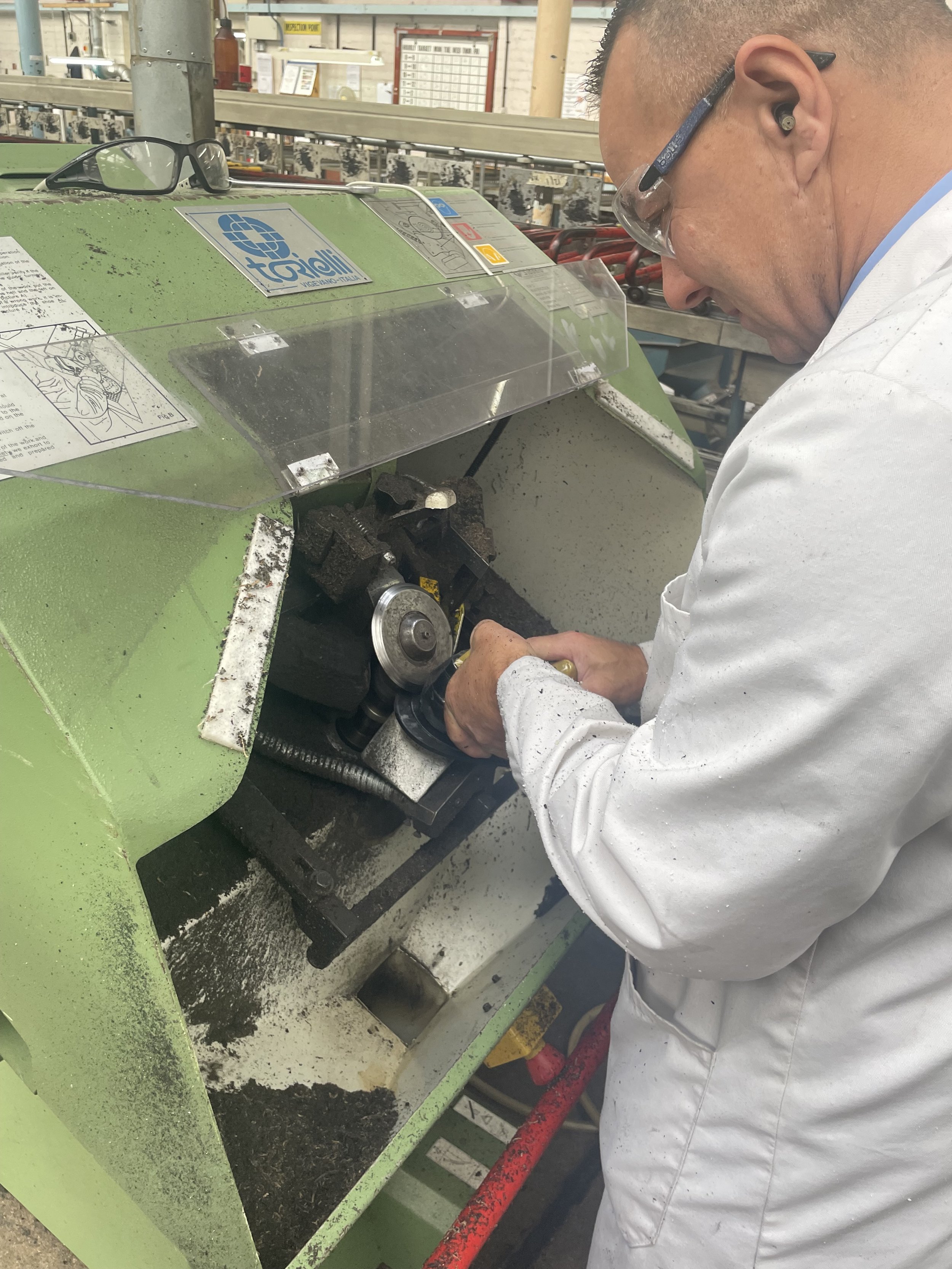
4. Finishing: The Final Touches
After the sole is stitched onto the welt, the shoe undergoes a series of finishing processes. This includes bottom leveling, where the sole is shaped and trimmed to match the last. The edges are carefully rounded, giving the shoe a clean, refined look.
In the final stage, the shoe is polished, buffed, and inspected for quality. The shoes are then left to rest, allowing the leather to fully set and conform to its new form. Before being prepared for customer delivery.
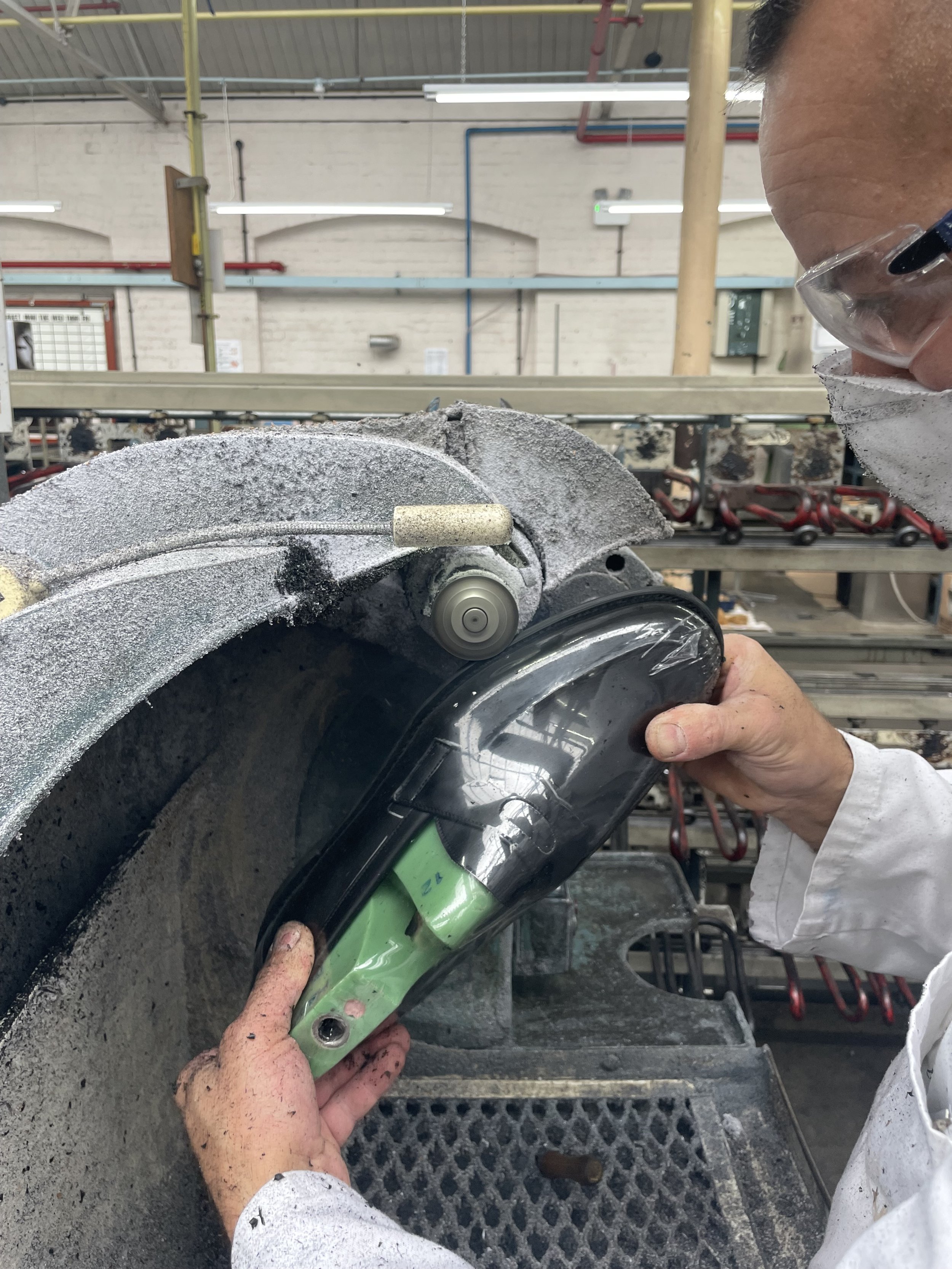
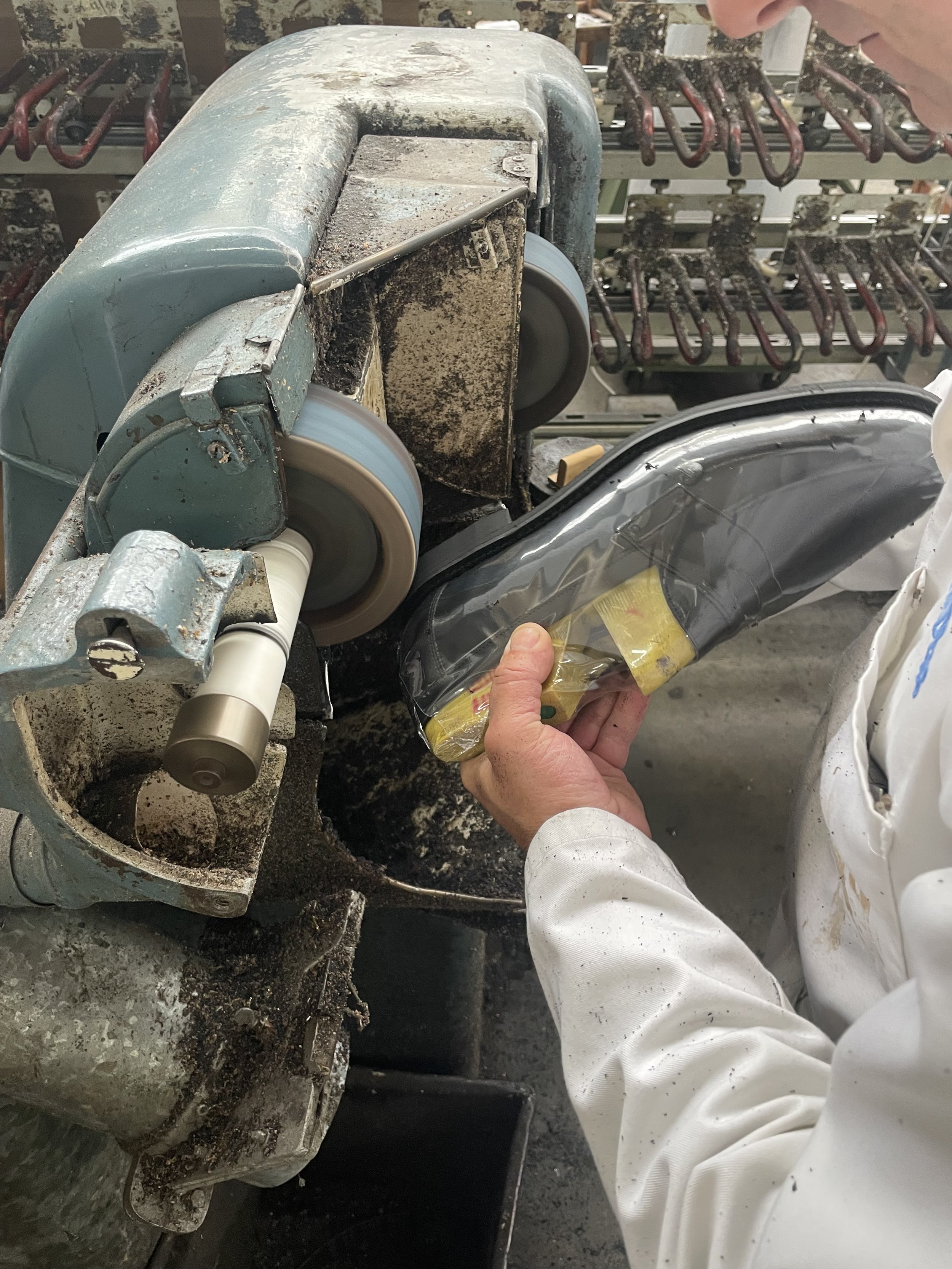
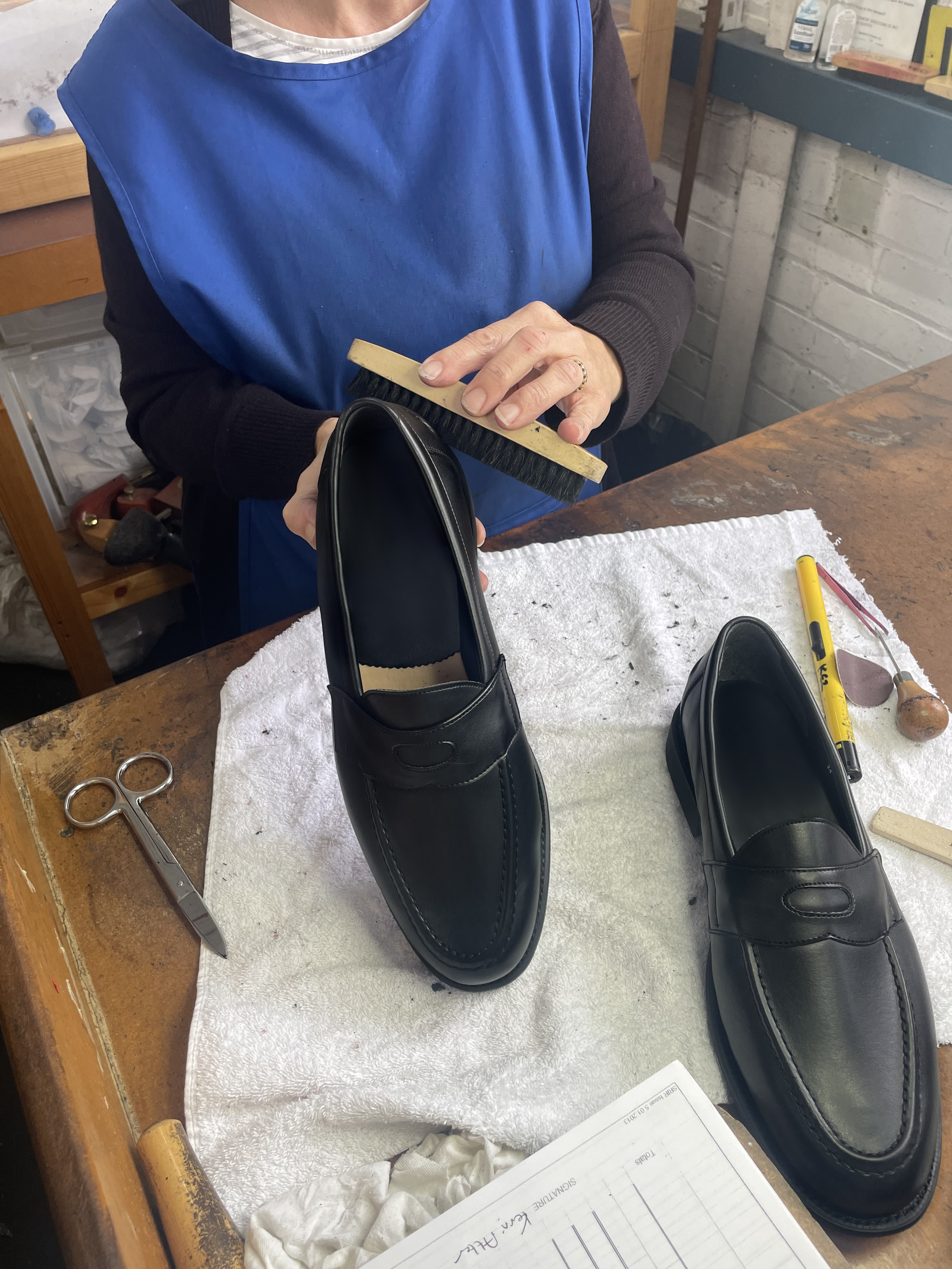
Published October 2024